Northwell Health Relies on Modular Devices Mobile Pharmacy Compounding Cleanrooms
In the fall of 2019, Northwell leadership assigned specific areas for upgrading, including the compound pharmacy in their Staten Island hospital. Great care and concentration had to go into the decision because of the protections needed for the life-saving work performed in this lab.
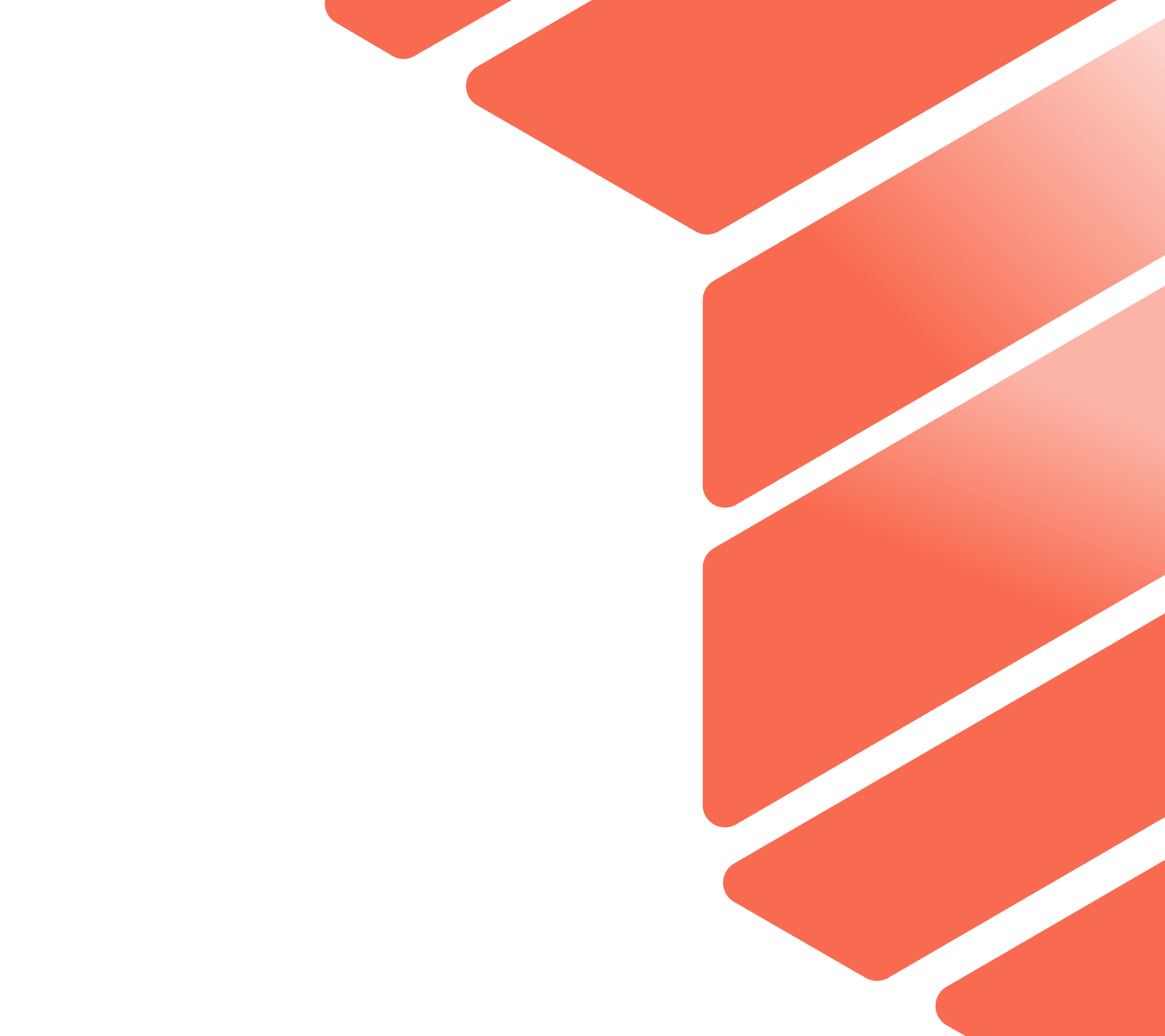
The Challenge:
Construction is disruption, which is an anathema for a hospital. Leadership at Northwell Health wanted a short lead time to open a modular lab, while upgrading facilities. Beyond all the regulatory requirements that they must meet, the facilities staff wanted an environmentally friendly lab that minimizes a carbon footprint.
Otto VonEilbergh, director, capital projects, corporate facilities services, Northwell Health, now knows first-hand all the intricate details of moving a unit that is 14 feet wide and 60 feet long and converting it into a high-tech, high-touch critical resource for a hospital. VonEilbergh managed the cleanroom installation, vendor details, and lab requirements.
“Getting a mobile unit through the streets and over the bridges in New York is a monumental undertaking. Various government entities require numerous permits and transport licensing,” said VonEilbergh.
The facilities team required a leveled foundation that would hold more than a 60 thousand pound trailer. It needed sterile materials and an uninterruptible power and water supply. They also had a lengthy list of to-dos to prepare for the State Board of Pharmacy to commission the mobile lab for compounding pharmaceuticals. The team continually balanced the need for speed with a systematic, measured approach to safeguards.
Northwell could not perform all of the requirements mentioned above without a vendor. Moreover, they were installing the lab in the middle of an unprecedented pandemic.
“For much of 2020, New York was at the epicenter of COVID-19. Everything went toward increasing patient capacity and acquiring equipment while still installing a lab,” said VonEilbergh. “To say we had challenges would be an understatement.”
The decision to contract with Modular Devices
The vendor requirements were numerous, which shortlisted the manufacturers. Northwell searched for a proven record in design, build, and certification of turnkey cleanroom installations. Vendors had to demonstrate how they could deliver a secure environment, uphold USP regulations, and maintain the production of compound pharmaceuticals with a written guarantee.
The clear choice became Modular Devices because of their vast experience in mobile labs, their array of services, and a complete understanding of the constraints and their plan on addressing them.
“The rental fees were reasonable for our marketplace,” said VonEilbergh. “Their statement of work met our requirements for this high-revenue department.”
Specifically, the chief pharmacy officer at Northwell Health applied the following criteria that solidified the contract with Modular Devices.
Design with the customer in mind
The pharmacy and facilities staff at Northwell Health noticed how the mobile unit on the concrete slab appeared nondescript. Upon initial inspection, they expected a 1980s infrastructure, but ended up walking through a sophisticated lab that looked like mission control at NASA. The well-laid-out design offered ergonomic functionality that delighted the pharmacy technicians.
“The bright white stainless covered every corner, exuding security and spotlessness,” said VonEilbergh. “The engineering team at Modular Devices also included smaller details that made big differences, such as the perfect placement for storage racks and digital displays.”
The engineers at Modular Devices applied its design-build method, which minimizes risk and expedites the project timeline by overlapping the design and construction phases.
Deliver a full-service compound pharmacy
“Modular Devices delivered on day one with turnkey capabilities. The only thing we had to do was turn on the water and connect the network and phones,” said VonEilbergh. “They provided an engineering timeline and coordinated with us four months ahead. Then, they delivered as promised.”
Modular Devices offerings didn’t stop with the fully functioning lab. They also oversaw all maintenance and certification programs. With their partner firms, pharmacy staff has access to ongoing training and emergency service.
Ensure compliance and safety
One of the most highly regarded areas of expertise for Modular Devices is ensuring compliance and certification with USP 797, the anticipated USP 800, and cGMP.
Before departing for New York, the cleanroom underwent a thorough quality control regimen and pre-certification. And upon completion of installation, the Modular Devices team prepared Northwell Health for inspection.
The mobile cleanroom met all regulations and codes, and the New York State Board of Pharmacy commissioned the lab. The commitment from Modular Devices didn’t stop after inspection. The team remotely monitors the lab from their headquarters in Indianapolis, IN. From downing to chemotherapy production, Modular Devices looked at all angles to ensure excellent safety protocols.
“I was impressed with the airlocks and humidity control infrastructure. And I was pleased when I received a call from Modular Devices saying check your pressures. Modular Devices remotely monitors the system so they knew before we did to review a setting,” said VonEilbergh. “They also supplied each room with a hands-free interlocking door with red and green light indicators to ensure the integrity of differential pressures.”
Maintain flexibility and deadlines
Modular Devices is the only mobile cleanroom provider that offers standard and customized mobile cleanrooms equally suited as either short or long-term rentals or a purchased unit. The Staten Island location went with a lease agreement.
The mobile cleanrooms came with 40 percent more space than other cleanrooms on wheels, providing more functional flexibility for personnel and workflow. Modular Devices can build their product in a fraction of the time as they control the entire production at their facility, eliminating delays caused by local permit approvals or subcontractor scheduling.
“Modular Devices met all deadlines and sped up the timeline,” stressed VonEilbergh. “And all of this was done during COVID-19. They just stepped up and worked through it, just like we did at the hospital.”
The results
The can-do team at Modular Devices provided exact specifications for the interim mobile compounding pharmacy, and then delivered on every one of them. Northwell Health even incorporated many of the design elements into their system, such as putting your hand up to the light beam to enter an area, having a highly controlled pass-through for pharmaceutical carts, and implementing motorized doors rather than a hinged door.
Upon delivery, the New York Board of Pharmacy conducted an inspection and approved the unit to compound both hazardous and traditional I.V. solutions for patients.
Northwell Health received a one-stop vendor for everything and beyond for a cleanroom. The products, services, and maintenance for the compounding pharmacy never faltered during the most tumultuous time for the hospital.
Although the hospital’s upgraded areas are complete, the mobile unit is still in use today because leadership extended the lease. Modular Devices actively monitors the unit and provides support to the pharmacy technicians.
Two brands.
One philosophy.
Modular Devices is a leading provider of mobile and modular imaging labs and cleanroom solutions, serving hospitals, surgery centers, compounding pharmacies, and life sciences organizations across the U.S.
Our turnkey Mobile Cath Labs, Modular EP Labs, Mobile MRI and CT Scanners are designed for rapid deployment and clinical precision. In parallel, our USP 797 and USP 800-compliant Mobile Cleanrooms and Modular cGMP Cleanrooms offer flexible, regulatory-ready environments for pharmaceutical compounding, biotech research, and sterile manufacturing. With nationwide delivery, expert support, and customizable configurations, we help healthcare and life sciences teams maintain continuity, compliance, and care—without compromise.